DR无损检测
来源:忠科检测
忠科检测提供的DR无损检测,DR(DigitalRadiography)无损检测,又称数字射线检测或数字X射线检测,出具CMA,CNAS资质报告。
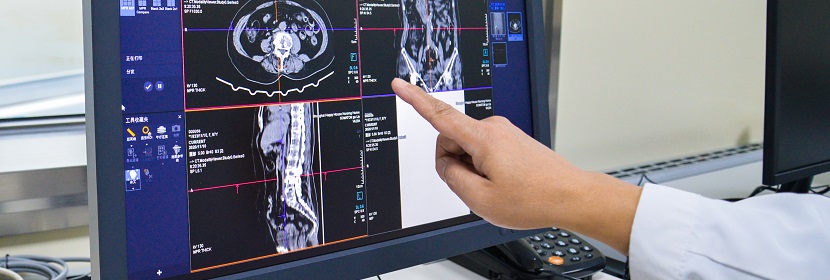
DR(Digital Radiography)无损检测,又称数字射线检测或数字X射线检测,是一种利用数字化X射线成像技术对材料或工件内部结构进行非破坏性检验的方法。在该检测过程中,X射线穿过被检测物体后,由探测器接收并转化为电信号,再经过数字化处理形成清晰的黑白图像,从而揭示出被检测物体内部的缺陷(如裂纹、气孔、夹杂物等)及其分布状况。
相比于传统的胶片射线照相检测,DR无损检测具有更高的检测效率和图像质量,能实现实时成像、动态观察以及图像后期处理等功能,且其辐射剂量较低,更加环保。广泛应用于航空航天、石油化工、电力、冶金、机械制造等领域的产品质量控制与安全评估中。
DR无损检测目的
DR(数字射线检测)无损检测的主要目的是在不破坏或不影响被检测对象完整性及使用性能的前提下,利用X射线或伽马射线穿透物体,并通过探测器接收和转换成数字图像,从而对物体内部结构、缺陷、材料性质等进行准确、快速的检测与评估。其具体目的包括:
1. 检测缺陷:如裂纹、气孔、夹杂、疏松、未熔合、未焊透等内在缺陷,确保工件的安全性和可靠性,如焊接件、铸件、锻件的质量控制。
2. 材料分析:了解材料的密度分布、厚度变化等特性,用于新材料研发、产品质量改进以及废旧零部件的剩余寿命评估等。
3. 过程监控:在生产过程中实时监测产品的质量状况,及时发现并纠正生产问题,提高生产效率和产品质量。
4. 法规遵从:对于某些特殊行业(如压力容器制造、航空航天、核能设备制造等),按照相关法规和标准要求必须进行无损检测以确保设备安全运行。
DR无损检测项目
DR(Digital Radiography,数字射线照相)作为一种先进的无损检测技术,在工业、建筑工程、航空航天等领域有着广泛的应用。DR无损检测项目主要包括以下几种:
1. 工业铸件检测:对各类金属铸件(如铸钢、铸铁等)、非金属铸件进行内部缺陷检测,如气孔、夹杂、疏松、裂纹等。
2. 焊缝检测:用于检测焊接接头的内部缺陷,如未熔合、未焊透、夹渣、气孔、裂纹等,确保焊接质量符合标准要求。
3. 压力容器及管道检测:对压力容器、管道等承压设备进行定期检测或在役检测,查找可能导致失效的缺陷。
4. 航空航天部件检测:对飞机零部件、火箭发动机组件等进行精细检测,确保其内部结构完整性。
5. 桥梁钢结构检测:用于桥梁、建筑钢结构等大型工程结构的无损检测,及时发现潜在安全隐患。
6. 铁路车辆及轨道交通部件检测:对铁路车辆轮轴、车钩、转向架等关键部件进行无损检测,保障运行安全。
7. 其他特殊应用:还可应用于文物考古、地质勘探、材料研究等领域,对样品进行内部结构分析和缺陷识别。
以上各项检测均能通过DR技术实现高精度、高效率的无损检测,为产品质量控制、设备安全评估提供有力的数据支持。
DR无损检测流程
DR(数字射线)无损检测流程一般包括以下几个主要步骤:
1. 需求确认与合同签订:
客户提出检测需求,包括被检对象、检测部位、预期的检测项目及标准等。
检测机构根据客户需求进行评估并提供检测方案和报价。
双方协商一致后签订服务合同。
2. 现场调查与准备:
检测人员赴现场进行前期勘查,了解被检对象的具体情况,确定检测方法和具体实施方案。
准备必要的DR检测设备,如数字射线机、影像板、防护设备等。
3. 工件制备与标记:
根据检测要求对被检工件进行必要的清理、打磨等工作,确保表面状态满足检测条件。
对检测区域进行准确标记和记录,以便后期图像分析。
4. DR拍摄与数据采集:
设置好DR检测参数,对被检工件进行多角度、多层次的射线曝光拍摄。
实时采集并存储数字射线图像数据。
5. 图像处理与分析:
利用专业软件对采集的DR图像进行调整、增强、拼接等处理。
通过对比分析,查找可能存在的内部缺陷或结构异常。
6. 结果评定与报告出具:
根据相关标准和规范,对检测结果进行科学、公正的评价。
编写详细的检测报告,包括检测方法、过程、结果以及建议等内容,并由具备资质的专业人士签发。
7. 交付与后续服务:
向客户提交检测报告,并解释说明检测结果。
如有需要,可针对检测结果提供进一步的技术咨询或解决方案。
以上流程仅为一般性描述,实际操作中可能会根据具体的检测项目和要求有所差异。同时,整个过程必须严格遵守国家有关法律法规和行业标准,保证检测的公正性和准确性。