金属失效分析
来源:忠科检测
忠科检测提供的金属失效分析,金属失效分析是对材料、零部件或结构在使用过程中因各种原因导致的性能下降、损坏或丧失原有功能的现象进行系统的研究和评估的过程,出具CMA,CNAS资质报告。
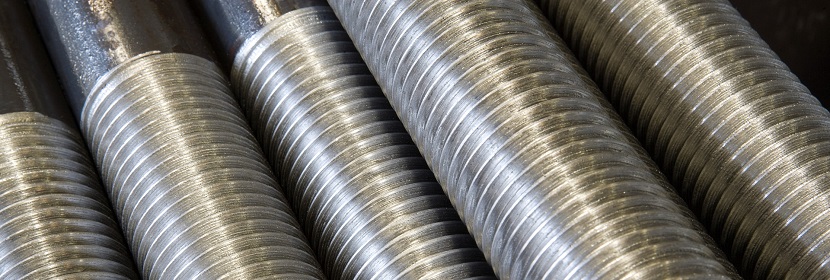
金属失效分析是对材料、零部件或结构在使用过程中因各种原因导致的性能下降、损坏或丧失原有功能的现象进行系统的研究和评估的过程。它通过一系列物理、化学、力学等检测手段,结合实际工况条件,找出金属失效的原因,并评估其安全性和可靠性,从而为改进设计、选择合适的材料、优化工艺流程、预防类似失效问题的发生提供科学依据。
失效模式可能包括断裂、磨损、腐蚀、疲劳、蠕变、氢脆、应力腐蚀开裂等多种形式。失效分析涵盖从宏观观察、微观检验到理论模拟等多个层次,目的是确保金属材料及其制品能够满足预期的设计要求和使用寿命,保障工业生产和工程设施的安全运行。
检测目的
金属失效分析的主要目的是通过对在使用过程中出现故障、损坏或性能下降的金属材料和制品进行系统、科学的研究,以确定其失效模式、失效机理及主要原因,并据此提出改进设计、选材、制造工艺或使用维护等方面的建议,防止同类失效问题的再次发生。具体来说,金属失效分析的目的包括:
1. 明确失效原因:通过观察、测试和分析,找出导致金属零部件或结构失效的直接原因和间接原因。
2. 防止失效重复发生:基于失效分析结果,优化设计,改进材料选择,提升制造工艺,或者调整运行维护策略,从而提高产品的可靠性和使用寿命。
3. 提升产品质量与安全性:通过失效分析了解产品潜在的风险和弱点,采取有效措施消除安全隐患,确保设备设施的安全稳定运行。
4. 节约成本:及时发现并解决失效问题,避免因设备故障引发的停机损失,降低维修和更换部件的成本。
5. 为新材料、新工艺的研发提供依据:通过对失效案例的研究,可以深入了解材料性能极限及其在实际工况下的行为特性,为新材料、新工艺的研发提供重要参考。
检测项目
金属失效分析项目通常是对材料、部件或结构在使用过程中由于各种原因导致的性能下降、损坏或丧失原有功能的现象进行深入研究和科学评估的过程。这个项目主要包括以下几个方面:
1. **失效模式识别**:观察并记录金属零部件失效的具体表现形式,如断裂、磨损、腐蚀、变形、疲劳等。
2. **宏观与微观检查**:通过肉眼观察、光学显微镜、扫描电子显微镜(SEM)、透射电子显微镜(TEM)等手段对失效部位进行详细检查,获取失效的初步信息。
3. **成分分析**:通过光谱分析、能谱分析(EDS)、波谱分析等方式确定金属材料的化学成分是否符合设计要求,是否存在异常元素或者杂质。
4. **力学性能测试**:包括硬度测试、拉伸试验、冲击试验、疲劳试验等,以评价材料的实际力学性能与其设计标准的符合性。
5. **金相组织分析**:通过金相显微镜观察失效部位的组织结构,判断是否存在过热、过冷、晶粒粗大、夹杂物、析出物等问题。
6. **环境影响因素评估**:考虑服役环境对金属材料的影响,如温度、湿度、腐蚀介质、应力状态等因素。
7. **失效机理分析**:基于以上各种测试结果,综合分析推断导致金属失效的根本原因,可能是设计不合理、制造工艺缺陷、选材不当、运行维护不善等。
8. **预防与改进措施建议**:根据失效分析结果,提出针对性的改进设计、优化工艺、加强监控等方面的改进建议,以避免类似失效情况的再次发生。
以上就是金属失效分析项目的常规内容,具体的分析流程和方法会根据实际失效情况和需求进行调整。
检测流程
金属失效分析流程通常包括以下几个步骤:
1. 接收到样品和背景信息:首先,检测机构会从客户那里接收需要进行失效分析的金属样品,并获取相关的使用环境、操作条件、失效模式、失效历史等详细背景信息。
2. 初步检查与记录:对样品进行外观检查,记录其尺寸、形状、颜色、表面状况(如裂纹、腐蚀、变形等)以及失效部位特征。
3. 非破坏性检验:通过无损检测方法(如超声波检测、磁粉探伤、渗透探伤、涡流检测、射线检测等)来确定缺陷的位置、大小及形态。
4. 微观结构分析:采用金相显微镜、扫描电子显微镜(SEM)、透射电子显微镜(TEM)等设备观察并分析样品的微观组织结构、夹杂物、析出物等。
5. 力学性能测试:根据需要进行硬度测试、拉伸试验、冲击试验、疲劳试验等相关力学性能测试,以评估材料的机械性能是否满足要求。
6. 化学成分分析:通过光谱分析、能谱分析、质谱分析等方式确定样品的化学成分是否符合标准或设计要求。
7. 模拟实验与仿真计算:在必要时,通过实验室模拟实际工况或者借助有限元分析等工具进行仿真计算,复现或预测失效过程。
8. 失效机理分析与结论提出:基于以上各种测试数据和结果,分析导致金属失效的根本原因,提出改进措施和预防建议,并撰写详细的失效分析报告。
9. 反馈与跟进:将失效分析报告提交给客户,并针对报告中的建议提供后续的技术支持和服务。
请注意,具体的失效分析流程可能会因不同的失效模式、材料类型、失效环境等因素而有所调整。